Managing the Defense Industry
Before the Second World War, there was a strong ‘America First’ political faction in the USA, which didn’t want to take part in foreign wars. However, President Franklin D Roosevelt realized that war was inevitable and he began ramping up the US industrial base to prepare for it.
The government owned over 100 facilities that made weapons and equipment but they wouldn’t be able to provide the volume that was needed so civilian factories were converted or created to fill the demand. However, military equipment required higher precision and quality than the civilian factories and workforce could manage, so the designs of the equipment had to be modular and simplified.
One example of that process was the B-24 bomber, designed by Consolidated Aircraft. While the design was state of the art, flying faster, farther and carrying a heavier payload than the famed B-17 made by Boeing, every single B-24 was individually hand-crafted. To increase production, the government enlisted the Ford motor company, which could quickly produce cars with 15,000 parts.
Of course, there were critics of this idea: they - rightfully - doubted they could manage the same feat with an aircraft that had 450,000 parts, including 360,000 rivets that came in 550 different sizes.
When Ford’s production chief saw Consolidated’s production process he noted that no two aircaft were built alike. In his hotel room he stayed up until 4 o’clock in the morning to design a new work flow process. In the pre-Digital Information era, his 70-man engineer team then spent six months trying to collect the specifications and plans for each component only to find out that the drawings were incomplete or marked with symbols only known to a few, and some of the knowledge only existed in the memories of a few workers. So they flew two B-24s to Michigan and dismantled them, working 24 hours a day, seven days a week for almost a year to create over 1.5 million square meters of three dimensional blueprints for 30,000 components. From that, they created 1,600 machine tools and 11,000 fixtures to repeatedly create parts with thousandths-of-an-inch tolerances.
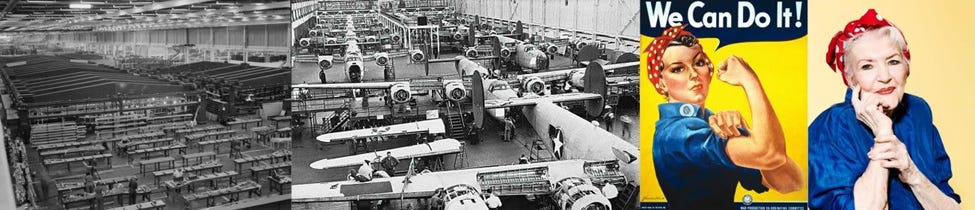
Ford had other issues to overcome. A 975x390 meter Willow Run plant was built in a rural area and there was not enough nearby housing for the eventual peak of 42,000 workers. Therefore, they provided housing for 15,000 employees and the government built a 60-kilometres-long expressway from Detroit to the plant. The hard steel dies used to stamp steel auto parts damaged the aluminum used in 85% of the aircraft; therefore, they had to be replaced. The first 56 planes that came off the assembly line by the end of 1942 were deemed unfit for combat and relegated to training, reconnaissance and transport duties. Constant performance and safety upgrades based on feedback from usage required delays caused by re-tooling. This was resolved by outsourcing more parts and subassemblies to nearly a thousand other factories that would retool when changes were required. The Willow Run plant itself would keep assembling the parts and components as they arrived without slowing down.
Eventually, the issues were resolved and the factory started turning out airplanes at a record pace. At its peak, Willow Run was completing another new aircraft every hour, and produced 8,645 in total - compared to the 9,808 planes made by Consolidated, Douglas Aircraft, and North American Aviation combined.
The concept of simple modular designs contributed to that mass production of other equipment, such as assembling a Liberty ship in 24 hours, or building 49,000 Sherman tanks in 41 months when Germany built that many tanks and assault guns throughout the entire war, with some parts individually crafted.
Even when an equipment design is complete it takes time to establish the supply lines to source the raw materials, build the components and then assemble them. Roosevelt recognized the need and used his political capital to ramp up production two years before the US entered the war. Production began ramping down before the war ended. With unmanned B-24s in reserve, the Willow Run plant closed on 28 June 1945.
With the Soviet Union emerging from the war as an adversary, the US Congress sought to maintain national production surge capability by preserving idle factories. However, it didn’t allocate any money for the program and the unmaintained facilities fell into disrepair. The US produced over 21 million shells calibre 105mm shells during the Second World War, but when the Korean War started, five years later, the demand for the shells exceeded the stockpiles, and the ramp up-in production was much slower than in 1941-1944. As a consequence, batteries operating guns calibre 105mm, have had their ammo rationed for two years before production finally caught up.
The Vietnam- and Cold Wars required high levels of production, but the demand dropped with the early 1970s when the Vietnam war wound down, and many US defense companies merged or went out of business. The end of the Cold War in 1989-1991, brought another round of consolidation. Whereas the US government owned 200 factories at the beginning of the Second World War, it was now almost entirely dependent on civilian defense production, and the consolidation of so many companies reduced competition and innovation. The days of the legendary Skunk Works and Higgins boats were replaced with expensive long-term development programs. Industrial capacity was lost, and with increased complexity it can now take 2-3 years to build a single tank. Only five large defense companies (Lockheed Martin, Boeing, General Dynamics, Raytheon and Northrop Grumman) survived the consolidations - and the barriers for manufacturing big projects, such as jet aircraft, are much bigger now than they were prior to 1941.
Roosevelt had the benefit of isolationism to ramp up US production before it entered the war but Ukraine and the West refused to acknowledge the threats of the 2008 invasion of Georgia, the 2014 invasion of Ukraine, and the gathering of Russian forces during the summer of 2021. In fact, during that summer of 2021, the US scaled back on the production of artillery shells calibre 155mm just to save money. Their stockpiles and production were sufficient to support 2.5 regional wars but were less than a tenth of what was needed to fight a near-peer adversary or support an ally that was in such a fight. Ukraine was also unprepared and they suffered for it.
While there were Ukrainian government programs, grass roots civilian efforts started creating technological tools to gather and share battlefield data, and volunteer groups started fund raising efforts to provide units with everyday essentials, such as generators, tourniquets and trucks. But one of the biggest impacts by civilians was when the hobby drones - used by just a few units since 2014 - became widely used as both reconnaissance and strike vehicles. Private manufacturers moved from ordering and assembling existing parts to designing and creating their own parts. Ukraine is incentivizing manufacturers to produce more than 50% of their parts locally. One company produces 70% of their components domestically and just released a batch of drones in which every component was built in Ukraine.
Funding came from both donations and the government, and the 500+ Ukrainian companies drove innovation and improvement cycles that are sometimes only two weeks long. When a UK company agreed to partner with Ukraine they realized that the fast pace of change can interfere with the rate of production so they agreed to incorporate new design changes no more than every six weeks.
The large numbers of drone companies spurred innovation and diversity in designs but a significant amount of innovation is coming from the Ukrainian soldiers. The large number of drone producers, coupled with a lack of manufacturing standards, is now costing time and money, and is slowing down innovation both at the front line and among engineers. In 2025 alone, Ukraine accepted 600 different types of weapons, including 250 models of drones and 100 types of ammunition. This is twice as many as in 2024.
The different models of artillery, tanks and other armored vehicles that Ukraine received from allies complicates logistical support. The same is true for drones that are domestically manufactured. Multiple components performing the same function are harder to scale for mass production than a single component. Software integration between systems is more difficult with varying designs and features. The testing and use of some models isn’t as extensive and issues such as battery fires emerged over time with some models.
There are multiple models of detonators and multiple models of ammo, many of which have threads that are incompatible with each other so they have to be returned to a lathe operator for re-threading in order to be screwed together. Different types of ammo lead to increased danger for the sappers that handle them.
With standardized models, such as the Mavic drone, it is easier to develop software and create modifications, such as combining batteries for longer flight times.
Different types of EW equipment also creates problems with training, operations, compatibility and maintenance. The NATO standard for color codes is green for normal operations, yellow for warning or unstable mode, red for critical failure and blue for encrypted mode, but some Ukrainian manufacturers use different colors to represent the same status. On top of that, power supplies, cables and antennas aren’t compatible with each other.
Ukraine’s drone industry has reached the stage where standards need to be gradually introduced and guided by experts while still retaining the flexibility needed for innovation and technological progress. New drone models are effective for about 2-6 months before the enemy adapts to them and reduces their effectiveness. Innovation is needed to maintain high levels of effectiveness. Standardization is needed for inexpensive mass production and open-ended interoperability that supports innovation.
Open-ended interoperability was a goal of a CEO of an AI firm who resigned to work with a team to create a better artillery shell. Tiberius Aerospace was founded in 2022 in response to the Russian invasion and since then they developed the Sceptre, a guided ramjet ballistic munition with a range of 140-160 km and an accuracy of 3.5 meters or less. It can be fired from any gun calibre 155mm at a cost $52,000, which can be reduced to $42,000 (or less) through mass production.
For comparison, GMLRS used by HIMARS has a 70 km range, cost $168,000. Arguably, it also has a 90Kg warhead compared to Sceptre’s 5.2Kg warhead. Excalibur 155 mm rounds cost at least $80,000. Excalibur uses GPS and inertial navigation and ceased being effective when the GPS signal was jammed and the inertial navigation wasn’t accurate enough by itself. Sceptre also uses GPS and inertial guidance but while Excalibur reached a maximum of 10,000 meters in altitude, the Sceptre reaches 20,000 meters where it supposedly can’t be jammed for that portion of its flight. During the flight the AI coordinates between the GPS and inertial guidance navigation systems to correct the trajectory with higher confidence, and in-flight communication to aid in navigation is also available if the GPS is jammed. Since the ramjet does not fire until after it leaves the barrel, the Sceptre round has the same barrel-wear characteristics as a conventional 155 mm round.
This has the potential to be another useful tool on the battlefield, however, another innovation from the CEO isn’t just the weapon itself. It is how it is produced. After initial US production, he plans to license the manufacturing rights for $5 million for the initial year and $2.5 million for each year after. The company will provide specifications of the round’s components and software to the manufacturers who are then encouraged to innovate and modify. Any changes will be tested and certified by Sceptre and if it passes safety and efficacy standards it will be approved for production.
Since the manufacturing process is fairly simple it is a lower barrier for smaller companies to enter the defense production environment, and greater participation will increase industrial capabilities and innovation.
But this level of open-source production hasn’t been tried before and there could be problems. The certification process could be cumbersome. If a smaller company’s supply chain relies on a country such as China, like Ukraine used to be with drones, that country could cut off supplies. And just as civilian companies had to be educated on precise military tolerances in WW2, new companies need to be educated in handling explosive materials.
Then there are some weapon components that are still vital, but are specialized and expensive to build, creating a barrier for even large defense companies. Because of that, the US government still owns 23 weapons facilities. Watervliet Arsenal in New York state is the oldest and has been continuously operated since 1812. In 1889 it began making artillery barrels and built 2500 per month in WW2. Most of the equipment is 20 years past the obsolete state. Some of it was replaced in 2021, but in 2023 the government decided to spend $1.7 billion to modernize the entire facility. It currently takes up to four months to build a barrel from a steel cylinder. Automated production will increase the quality of the barrels and increase the production rate from 11 barrels a month to 18 barrels a month in 2025. Many of the barrels are shipped to the BAE subsidiary in the US for use on the M777 howitzer. The US will outfit their military with some foreign-designed equipment but only with the provision that they can produce it in the US under license so they are not dependent on foreign production during wartime.

Eventually, every country or security collective has to manage production capacity and the cost to maintain that capacity. It has to have an industrial base broad enough to encourage innovation and standards that allow interoperability. It needs to ensure that its supply sources cannot be threatened by a potential adversary. And it needs the political wisdom and will to ensure that its stockpiles are large enough to sustain its military until production is increased to a level that can supply its armed forces for the duration of the conflict.